A quick checklist for the implementation of AI in Manufacturing
Today industrial sectors, manufacturing systems, supply chains and production infrastructures are highly complex: products often consist of a large number of parts and components, and are manufactured using equally numerous and sophisticated manufacturing steps and various assembly and sub-assembly processes. In factories, interdependence and complexity of production processes increase the likelihood of downtime on the lines.
To manufacture, manage and maintain such infrastructures, it is necessary to develop a digital upgrading, capable of simulating and predicting the functioning of the system, to establish how equipment, machinery, processes, products must be designed, manufactured, and managed to operate at their best.
Artificial intelligence (AI) has made its foray into our lives and businesses in recent years. AI quickly interprets and learns from data to provide predictions and identify trends. For manufacturers, this technology proves especially vital. Manufacturers generate more data than any other business sector, but they also waste the most data. AI can help manufacturers leverage the full value of big data to improve decision making.
Although recognizing the power of this technology, ERP vendors are introducing AI in their software to give manufacturers an all-in-one solution for managing enterprise data and processes. However, manufacturers are still unsure how to incorporate AI into their everyday practices. To guide you in capitalizing on AI capabilities, we’ve provided a checklist on how AI can help manufacturers on the shop floor and listed some of the benefits of AI for manufacturing.
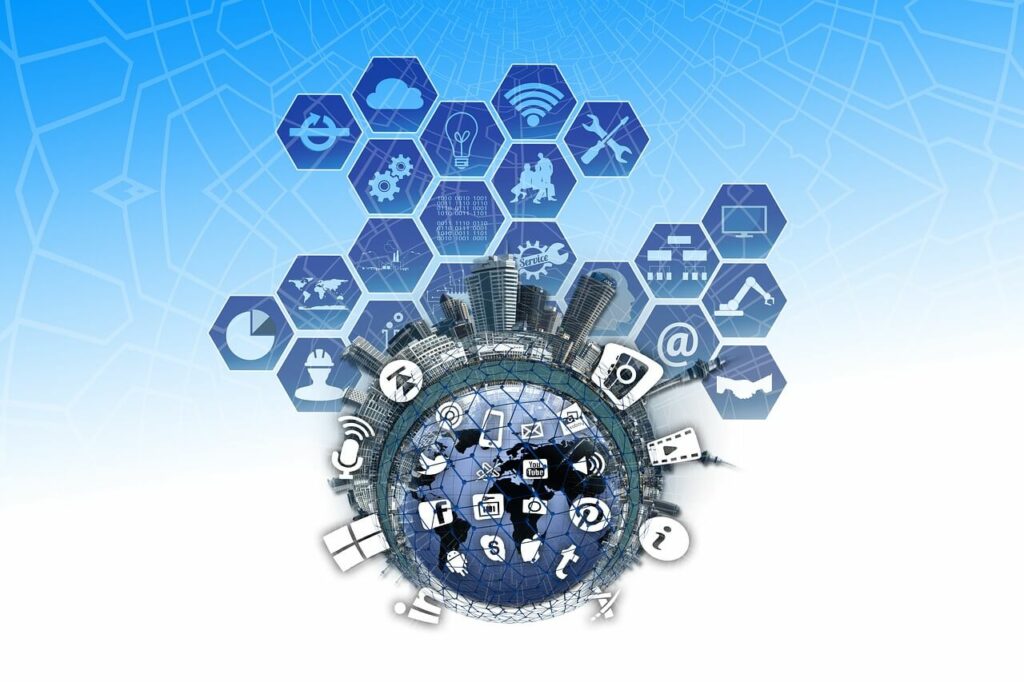
10 AI benefits
- Natural language processing (NLP) and virtual agents make it easier for users to access data and execute tasks. Users can interact with AI-powered virtual agents via voice or text to gain real-time insights and notifications.
- Using AI, manufacturers can evaluate the condition of equipment and predict when maintenance should be performed. When you use machine learning for predictive maintenance, you can reduce unplanned machinery downtime and maintenance costs by 30%.
- AI provides 360-degree visibility across plants, lines and warehouses. This gives users insights to detect quality issues, reduce scrap and make other production improvements. This helps manufacturers increase production throughput by 20% and increase quality by 35%.
- AI optimizes production planning and scheduling, even for complex manufacturing processes. It analyzes material availability, production capacity and customer demand to recommend the best scheduling plan.
- Instead of manually counting inventory, you can utilize AI to analyze inventory and maintain appropriate stock levels. This helps your business reduce costs and waste.
- Algorithms can accurately predict shipping and delivery lead times to improve the customer experience.
- Deep-learning-based systems enable up to 90% improvement in defect detection, ensuring you maintain pristine product quality.
- AI simplifies manufacturing operations by fully automating complex tasks and requiring less manpower to maintain. It also gives businesses the agility to quickly revise production plans or immediately adjust material flow based on schedule or product changes.
- This technology improves employee productivity by making critical insights easily accessible. Engineers can immediately locate the type of material that should be used for a specific product, and manufacturers can use reports to predict orders.
- By automating repetitive processes and increasing visibility, AI delivers a better user experience. Employees can spend more time on enjoyable tasks, rather than perform mundane activities that could result in injury or fatigue.
Only companies that have the foresight to question their current business model by rethinking their problem solving strategies, failure analysis and the ability to deal with constant change and novelty will be able to reap the rewards and benefits of new technology implementations.
The publication of this article has been extracted and freely adapted from datixinc.com article by Jessica Staley